Why Should You Utilize a Preventive General Maintenance Checklist?
'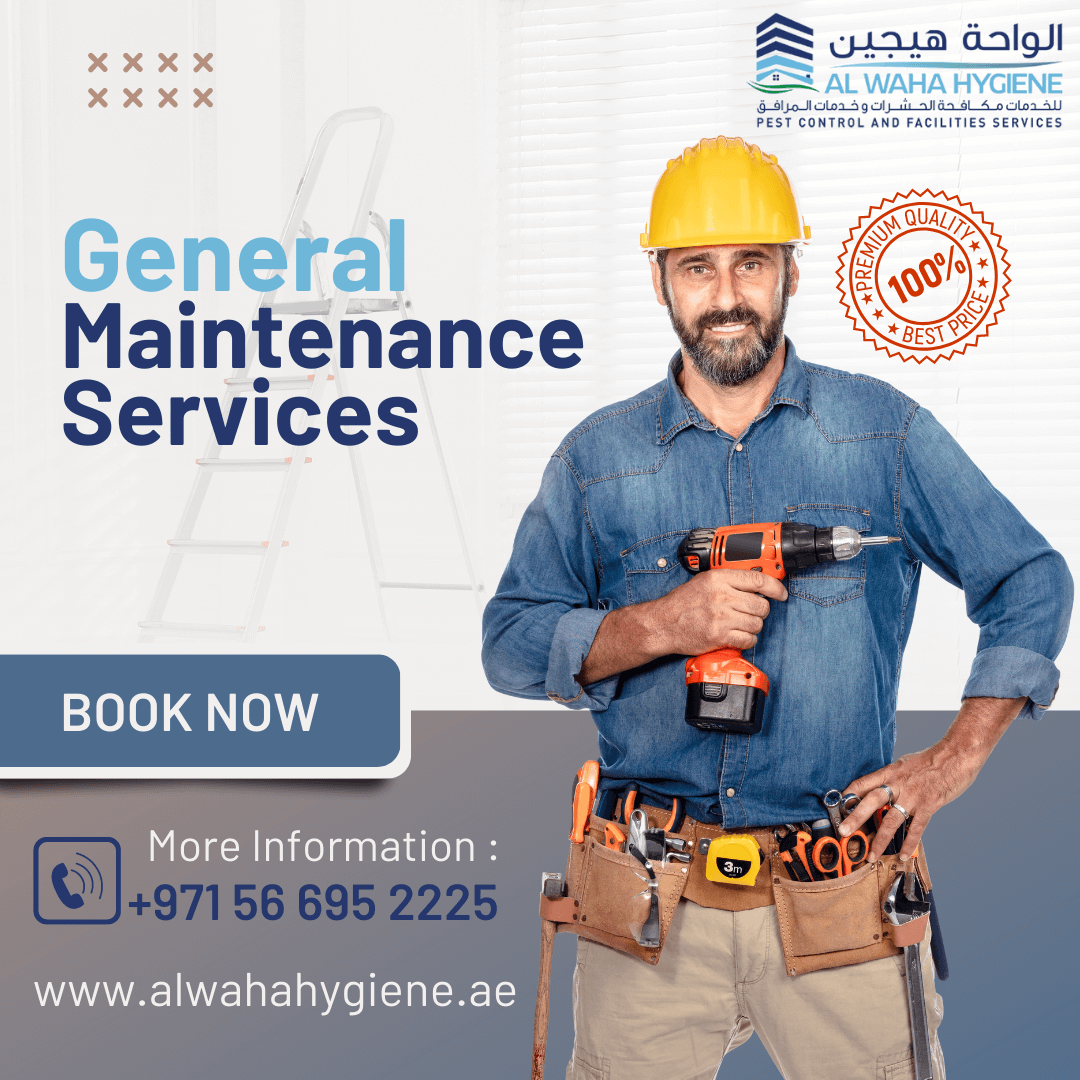
Creating a comprehensive template that outlines all the maintenance tasks for each equipment piece significantly simplifies the responsibilities of your maintenance crew. Additionally, a checklist enables technicians to methodically mark off each task as they progress through the list.
The main objective of implementing a planned General maintenance program is to minimize downtime and prevent costly emergency breakdowns. By using a checklist, factory maintenance technicians can effectively prioritize their focus on the appropriate tasks at the right intervals.
Having a general checklist of maintenance activities ensures that your maintenance personnel stay on track. Moreover, it assists managers in organizing the necessary resources, parts, tools, and supplies required for each work order.
How to Generate a General Task List
Determining Task Categorization
Depending on your business, you can categorize task lists for preventive maintenance operations in various ways. Both ongoing and ad-hoc maintenance work can be managed using separate lists tailored to specific purposes.
Certain maintenance services utilize three distinct task lists:
- General Maintenance Task List
- Equipment Task List
- Functional Location Task List
While this offers some level of organization, it can be challenging for businesses to manage and administer consistently.
For most businesses, beginning with a straightforward approach is crucial to ensure all stakeholders embrace a new method of managing maintenance tasks. Therefore, a more straightforward solution involves general checklists focusing on each equipment item or specific area within your facility.
For instance, you can streamline maintenance activities for areas such as driveways, walkways, and fences by utilizing a general exterior maintenance list. As your team becomes familiar with the checklist procedures, you can gradually break down the lists into more detailed sections.
Creating a Checklist for Each Asset or Machine
Regardless of the categorization system you adopt, it is likely that you will have numerous equipment pieces that necessitate regular inspections and periodic preventive maintenance. Examples include:
- HVAC systems requiring air filter changes at specific intervals
- Regular clearing of gutters and downspouts to prevent blockages and minimize fire hazards
- Monitoring boilers, water heaters, and pipes for corrosion, as well as ensuring proper calibration of thermostats at specific intervals
- Periodic checks by authorized technicians for fire extinguishers and carbon monoxide detectors
Developing a maintenance or inspection task list for each asset empowers your maintenance team with a replicable, structured process to follow.
Linking Your General Maintenance Task List to a Standard Operating Procedure
Integrating your checklist into a standard operating procedure (SOP) completes the maintenance plan and ensures that teams utilize checklists at the appropriate times.
Creating comprehensive SOPs is pivotal for running a productive and efficient business. By incorporating work orders into the equation, your maintenance department can function seamlessly and consistently in no time.
Professional General Maintenance Services in Abu Dhabi
Our approach to providing the highest quality general maintenance services from AC / HVAC installation and repair services, electrical services, motor rewinding, painting, plumbing, and handyman work is very simple. It’s about trust, completeness, and ability. That’s what you get every time at AlWaha Hygiene General Maintenance. It led our principles from day one. As a result, thousands of facilities in the United Arab Emirates (Abu Dhabi, Dubai, Sharjah, Ajman) have consistently been selected for essential and aesthetic work of all sizes.